System połączeń rowkowanych
System połączeń rowkowanych to rozwiązanie stosowane w sieciach technologicznych i pożarowych. Umożliwia szybkie i bezpieczne łączenie rur bez konieczności spawania. Atutami są szybkość montażu, niezawodność, szczelność oraz odporność na wysokie ciśnienie.
Z czego składają się systemy połączeń rowkowanych?
System rowkowany składa się z elementów tworzących solidne i trwałe instalacje. Podstawowym komponentem są rury rowkowane z odpowiednio wykonanymi wgłębieniami, które umożliwiają łączenie bez gwintowania czy spawania. Kluczową rolę odgrywają także złączki rowkowane do rur – zapewniają szybki oraz bezpieczny montaż.
W systemach wykorzystuje się również kształtki rowkowane, takie jak kolana, trójniki i redukcje, umożliwiające dowolne prowadzenie instalacji zgodnie z założeniami projektowymi. Dla zachowania pełnej funkcjonalności sieci niezbędne są także rowkowane zawory (armatura) umożliwiające regulację przepływu medium. Szczelność i trwałość połączeń zapewniają specjalne uszczelki oraz obejmy, które absorbują drgania i kompensują naprężenia.
Jakie zastosowanie mają systemy połączeń rowkowanych?
Rowkowane systemy rurowe najczęściej wykorzystuje się w instalacjach przeciwpożarowych, jak i technologii grzania i wody lodowej, oraz sprężonego powietrza, czyli tam, gdzie istotną rolę odgrywa szybki montaż oraz możliwość bezpiecznej rozbudowy systemu. Z kolei dzięki wysokiej odporności na ciśnienie produkty te znajdują zastosowanie również w rurociągach przemysłowych – m.in. w instalacjach do transportu wody, sprężonego powietrza, gazów technicznych czy olejów. Są także chętnie wykorzystywane przy modernizacji sieci wodociągowych, ponieważ umożliwiają szybką wymianę i naprawę istniejących rurociągów bez konieczności kosztownych i czasochłonnych prac spawalniczych.
Marki w naszej ofercie
Nasze realizacje: Sieci kanalizacyjne
Dostarczamy materiały wszędzie tam, gdzie jesteśmy potrzebni. Pomagamy realizować inwestycje na terenie całego kraju.
Zobacz pozostały
asortyment z kategorii
Instalacje p.poż.
Zamawiaj tak, jak Ci wygodnie!
Jesteś zainteresowany współpracą?
Zostań naszym klientem
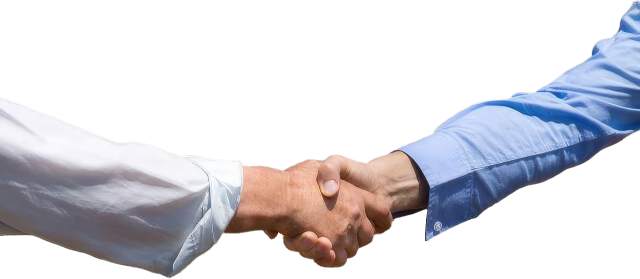
Dołącz do rodziny HTI i korzystaj z wieloletniego doświadczenia naszej Grupy!
Materiały używane w systemach połączeń rowkowanych
Materiały używane w systemach połączeń rowkowanych
Elementy systemu połączeń rowkowanych produkuje się przede wszystkim z żeliwa sferoidalnego (GGG40/50), dzięki czemu są dostosowane do różnych warunków eksploatacyjnych. Materiał wyróżnia się wysoką wytrzymałością mechaniczną, a stosując odpowiednie powłoki ochronne również wysoką odpornością na korozję, co czyni je popularnym wyborem w instalacjach wodnych i przeciwpożarowych. Z kolei stal węglowa jest powszechnie stosowana w rurociągach przemysłowych. Zapewnia trwałość i odporność na wysokie ciśnienie. Natomiast stal nierdzewna stanowi najlepszy wybór dla środowisk agresywnych chemicznie (przemysł spożywczy czy farmaceutyczny). Zapewniamy też produkty z aluminium, które znajdują zastosowanie np. w systemach wentylacyjnych. Coraz większą popularność zyskują również systemy rowkowane z tworzyw sztucznych. Są one odporne na korozję i chemikalia, a jednocześnie charakteryzują się niewielką masą i łatwością montażu.
Systemy rowkowane: szybki montaż i niezawodność w instalacjach technologicznych
Systemy rowkowane: szybki montaż i niezawodność w instalacjach technologicznych
Systemy rowkowane dostępne w naszej ofercie cechują się łatwym i szybkim montażem, który nie wymaga spawania ani specjalistycznych narzędzi, co w znaczący sposób skraca czas wykonania danej instalacji. Dzięki temu instalacje mogą być modyfikowane oraz rozbudowywane bez dużych nakładów czasowych i finansowych. Kolejną istotną zaletą jest również odporność na ciśnienie, co zapewnia niezawodne działanie nawet w wymagających warunkach. Systemy te charakteryzują się także odpornością na drgania i zdolnością do kompensacji naprężeń, co ma szczególne znaczenie w instalacjach wielkopowierzchniowych oraz w przemyśle ciężkim. Równie ważnym atutem tej technologii jest bardzo łatwy serwis poszczególnych elementów oraz sprawna naprawa konkretnych punktów instalacji, co przekłada się na niższe koszty utrzymania i większą elastyczność eksploatacyjną.